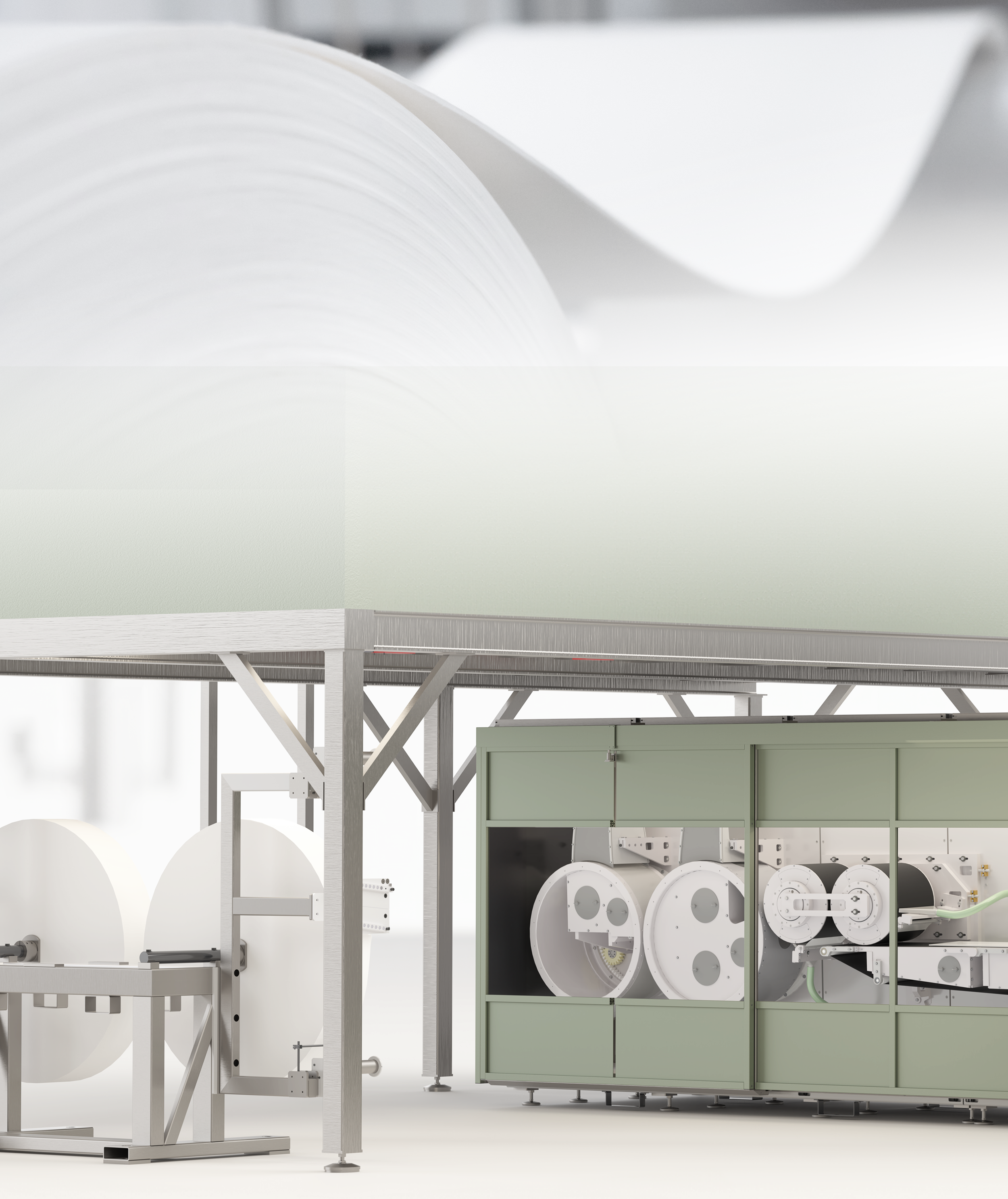
EXPERIENCE
dry forming excellence
We’re not just here to introduce you to new technology — we’re here to stand by your side every step of the way. From the first spark of an idea to a fully continuous production line, we’re all about building something real, together.
At our core, we believe in long-lasting relationships. We take ownership of our technology and the solutions we provide, but our commitment goes way beyond that. It’s about supporting you in your success, through every challenge and every breakthrough. Your goals are our goals, and we’re dedicated to helping you achieve them.
IT’S NOT JUST A MACHINE; IT’S A TRANSFORMATIVE SOLUTION BACKED BY OUR ADVANCED INDUSTRIAL PLATFORM THAT DELIVERS UNPARALLELED RESULTS.
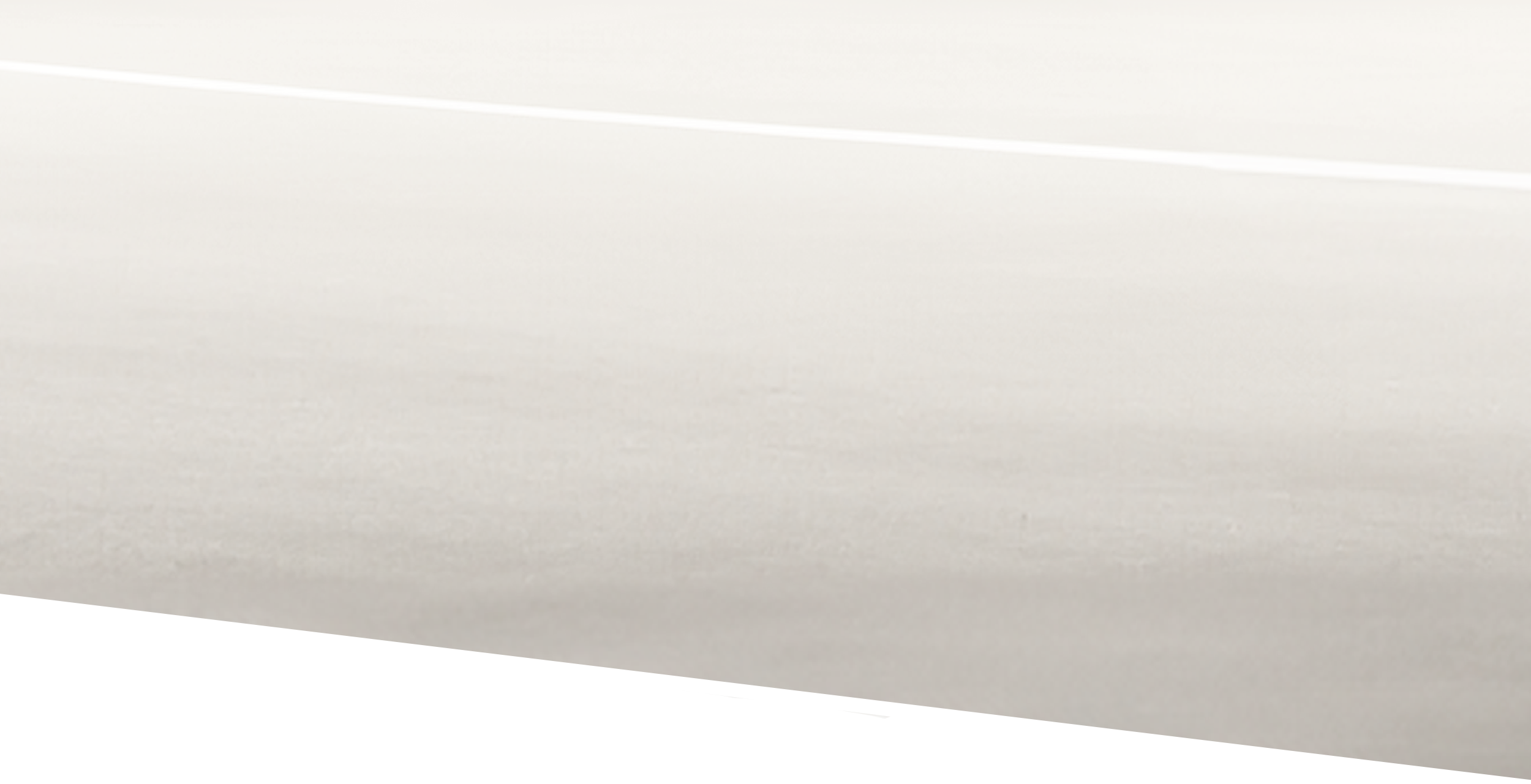
YANGI CELLERA:
A MACHINE AHEAD OF ITS TIME
Imagine a world where packaging innovation is just a step away — that’s what our Yangi Cellera technology makes possible. Our sleek machine line takes cellulose pulp and turns it into 3D-formed packaging consistently and efficiently, all at a lower cost than traditional fiber methods, and reduces your company's footprint in the process.
Why settle for the old when you can embrace the new? Yangi Cellera is designed to offer quick changeovers, great product flexibility, and a versatility in material possibilities that keeps you ahead of the curve. It’s cost-efficient, easy to operate (one person can manage two machines!), and ready to go with instant startup.
18x10x5.5
Machine Footprint (m)
4.5
Cycle Time (s)
850x450
Press Table Size (mm)
Proprietary Machine Platform
High Machine Availability
High Material Utilization
Low Cycle Time
Consistent Product Performance
300/450
Press Force (Ton)
DRY FORMING MADE SIMPLE:
THE ESSENTIALS
Dry forming with Yangi Cellera™ isn’t just about using pulp in packaging; it’s a transformative force for cellulose fibers. By combining two core technologies—airlaid fiber technology with 3D dry forming, we produce top-notch fiber-based packaging that fits right into existing recycling systems. And, with zero added process water and lower energy use, it conserves our precious resources and slashes CO₂ emissions by a cool 70%.

BEYOND 1-TO-1 REPLACEMENT:
FROM CONCEPT TO PRODUCT LAUNCH
With over a decade of expertise in dry forming and packaging design, you can trust that we know what our technology can deliver—right now. You’re not just getting a simple 1-to-1 replacement; you're partnering with a team that works closely with you to create tailored solutions that truly stand out.
With a fully industrialized platform at your disposal, you can confidently prove the technology's large-scale viability and launch compelling market offerings. Together, we'll explore new product possibilities, targeting both quick-to-market solutions and innovative features that push the boundaries of the technology and open up new product categories.
Secured Supply
Low Raw Material Footprint
Validated Fit-For-Purpose Recipes
The quality of pulp is key to getting superior products, and to keep things simple for you, we've forged strong relationships with suppliers so you get your materials on time and at the right price. We've also crafted unique chemical recipes, working closely with barrier and chemical experts, tailored specifically for our dry forming process.
After years of fine-tuning, our custom material recipes—pulp and chemistry—are proven to deliver. They maximize machine uptime and ensure your products consistently meet the highest standards.
CUTTING COSTS, NOT CORNERS:
PRECISION TOOLING DONE RIGHT
Our tooling solutions isn't just about delivering on the product's shape—its design must seamlessly integrate with every aspect of the dry forming process. It should align with the material recipe, guide pad geometry, and influence press placement and machine settings.
Designing a tool with us means getting a partner who’s all in on maximizing your machine’s output and boosting product performance. It's not just about having the right tool; it’s about having the right tool, designed affordably, to make your entire operation sing.
THE RIGHT MIX:
TAILORED RECIPES THAT DELIVER
EXPERIENCE
dry forming excellence
We’re not just here to introduce you to new technology — we’re here to stand by your side every step of the way. From the first spark of an idea to a fully continuous production line, we’re all about building something real, together.
At our core, we believe in long-lasting relationships. We take ownership of our technology and the solutions we provide, but our commitment goes way beyond that. It’s about supporting you in your success, through every challenge and every breakthrough. Your goals are our goals, and we’re dedicated to helping you achieve them.
IT’S NOT JUST A MACHINE; IT’S A TRANSFORMATIVE SOLUTION BACKED BY OUR ADVANCED INDUSTRIAL PLATFORM THAT DELIVERS UNPARALLELED RESULTS.
YANGI CELLERA: A MACHINE AHEAD OF ITS TIME
Imagine a world where packaging innovation is just a step away — that’s what our Yangi Cellera technology makes possible. Our sleek machine line takes cellulose pulp and turns it into 3D-formed packaging consistently and efficiently, all at a lower cost than traditional fiber methods, and reduces your company's footprint in the process.
Why settle for the old when you can embrace the new? Yangi Cellera is designed to offer quick changeovers, great product flexibility, and a versatility in material possibilities that keeps you ahead of the curve. It’s cost-efficient, easy to operate (one person can manage two machines!), and ready to go with instant startup.
Proprietary Machine Platform
High Machine Availability
High Material Utilization
Low Cycle Time
Consistent Product Performance
18x10x5.5
Machine Footprint (m)
850x450
Press Table Size (mm)
300/450
Press Force (Ton)
4.5
Cycle Time (s)
DRY FORMING MADE SIMPLE: THE ESSENTIALS
Dry forming with Yangi Cellera isn’t just about using wood pulp in packaging; it’s a transformative force for cellulose fibers. By combining two core technologies—airlaid fiber technology with 3D dry forming, we produce top-notch fiber-based packaging that fits right into existing recycling systems. And, with zero added process water and lower energy use, it conserves our precious resources and slashes CO₂ emissions by a cool 70%.
BEYOND 1-TO-1 REPLACEMENT: FROM CONCEPT TO PRODUCT LAUNCH
With over a decade of expertise in dry forming and packaging design, you can trust that we know what our technology can deliver—right now. You’re not just getting a simple 1-to-1 replacement; you're partnering with a team that works closely with you to create tailored solutions that truly stand out.
With a fully industrialized platform at your disposal, you can confidently prove the technology's large-scale viability and launch compelling market offerings. Together, we'll explore new product possibilities, targeting both quick-to-market solutions and innovative features that push the boundaries of the technology and open up new product categories.
The quality of pulp is key to getting superior products, and to keep things simple for you, we've forged strong relationships with suppliers so you get your materials on time and at the right price. We've also crafted unique chemical recipes, working closely with barrier and chemical experts, tailored specifically for our dry forming process.
After years of fine-tuning, our custom material recipes—pulp and chemistry—are proven to deliver. They maximize machine uptime and ensure your products consistently meet the highest standards.
THE RIGHT MIX: TAILORED RECIPES THAT DELIVER
Secured Supply
Low Raw Material Footprint
Validated Fit-For-Purpose Recipes
CUTTING COSTS, NOT CORNERS: PRECISION TOOLING DONE RIGHT
Our tooling solutions isn't just about delivering on the product's shape—its design must seamlessly integrate with every aspect of the dry forming process. It should align with the material recipe, guide pad geometry, and influence press placement and machine settings.
Designing a tool with us means getting a partner who’s all in on maximizing your machine’s output and boosting product performance. It's not just about having the right tool; it’s about having the right tool, designed affordably, to make your entire operation sing.
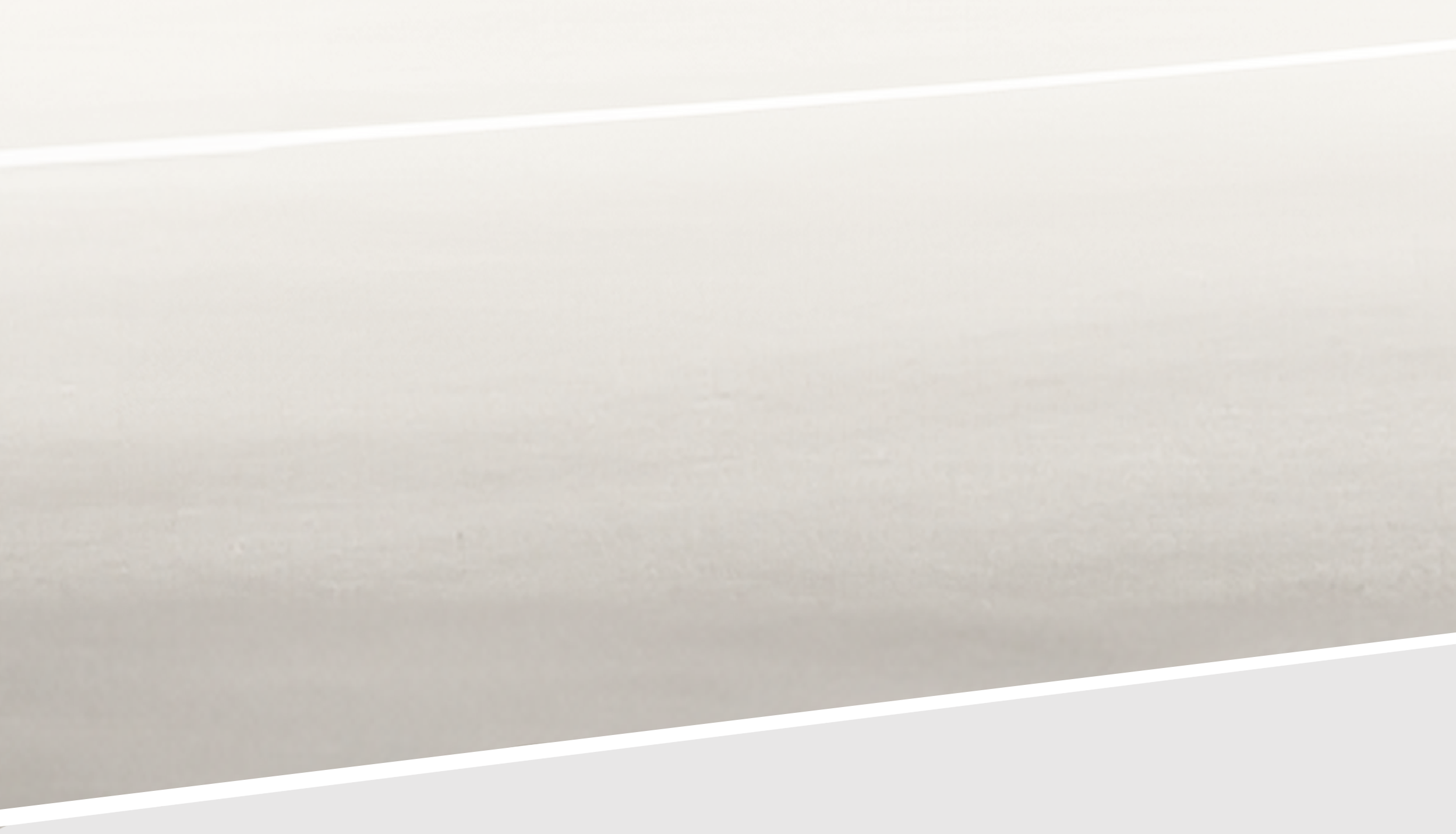
LET’S UNITE TO IGNITE:
EXPLORING NEW HORIZONS
PROTOTYPE FIRST
With our unmatched expertise in fiber-based packaging, we're here to help you unlock the potential of dry-formed solutions, creating packaging concepts that align perfectly with your business vision.
PROGRESS TOGETHER
We believe true impact comes from collaborating with our customers and partners, growing together to create sustainable, future-proof solutions that benefit both nature and business.
When we team up, we don’t just innovate—we redefine the status quo for a better tomorrow. By harnessing our growing network of game-changing partners from machines and tooling to materials and barriers, and inviting others to follow suit, we're leading the charge in fiber-based packaging. Let’s team up, shake things up, and together, create a new packaging standard for the future.
PUSHING BOUNDARIES
By combining fresh thinking, decades of experience, and a focus on co-creation, we work hand-in-hand with out clients and partners to unlock the full potential of dry forming technology.
WE PROMISE IT’S NEVER BORING
STAY IN THE LOOP, JOIN OUR JOURNEY:
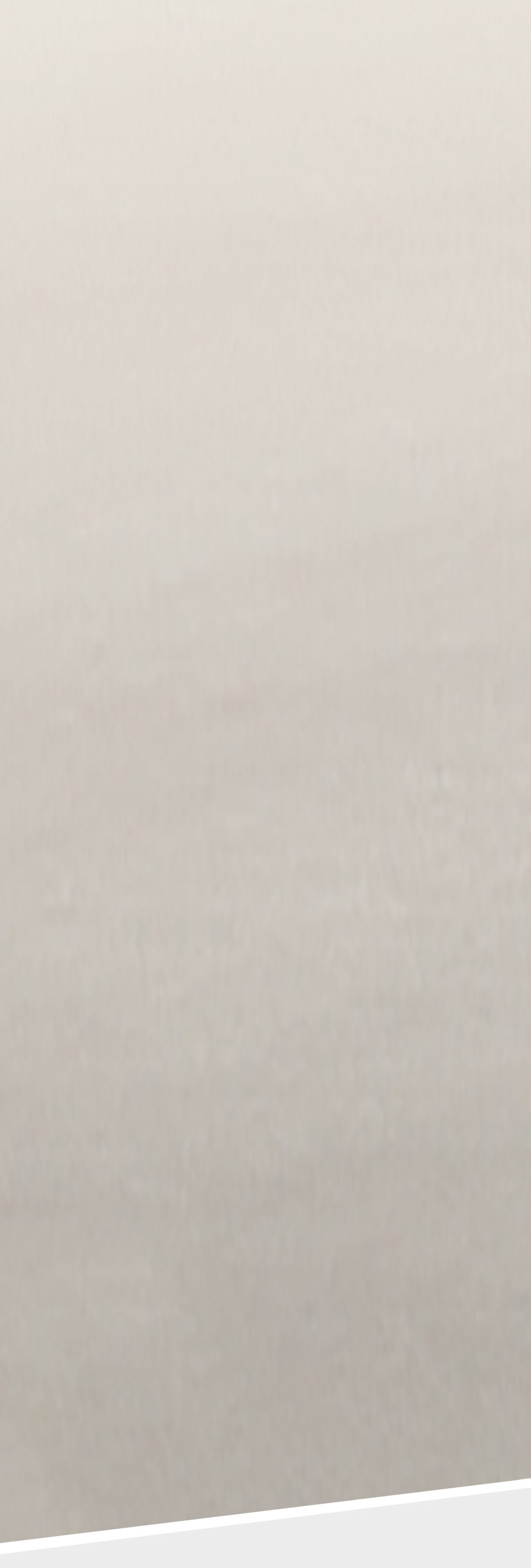
LET’S UNITE TO IGNITE: EXPLORING NEW HORIZONS
PROTOTYPE FIRST
With our unmatched expertise in fiber-based packaging, we're here to help you unlock the potential of dry-formed solutions, creating packaging concepts that align perfectly with your business vision.
PROGRESS TOGETHER
We believe true impact comes from collaborating with our customers and partners, growing together to create sustainable, future-proof solutions that benefit both nature and business.
PUSHING BOUNDARIES
By combining fresh thinking, decades of experience, and a focus on co-creation, we work hand-in-hand with out clients and partners to unlock the full potential of dry forming technology.
When we team up, we don’t just innovate—we redefine the status quo for a better tomorrow. By harnessing our growing network of game-changing partners from machines and tooling to materials and barriers, and inviting others to follow suit, we're leading the charge in fiber-based packaging. Let’s team up, shake things up, and together, create a new packaging standard for the future.
STAY IN THE LOOP, JOIN OUR JOURNEY: WE PROMISE IT’S NEVER BORING